Understanding the Benefits of Buying Injection Plastic Molds
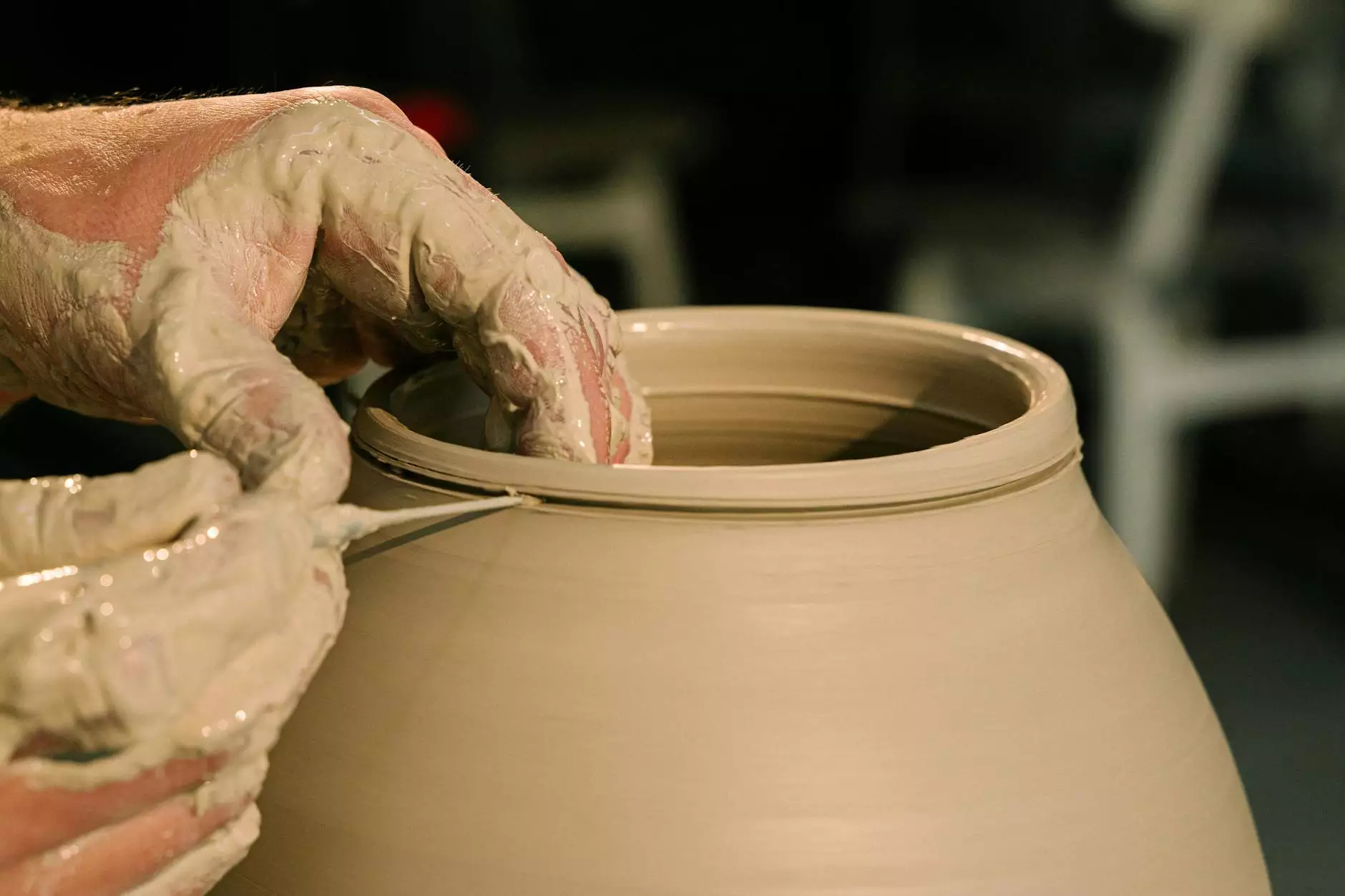
When it comes to modern manufacturing processes, buying injection plastic molds has become a crucial business decision for companies seeking efficiency and precision. The process of injection molding allows manufacturers to produce high-quality plastic components in large volumes while maintaining a significant level of detail. This article explores the various aspects of purchasing injection plastic molds, their benefits, and how they significantly impact production in the manufacturing sector.
What are Injection Plastic Molds?
Injection plastic molds are specialized tools used in the injection molding process, where molten plastic is injected into a mold to create various plastic parts. The molds themselves are typically made out of durable materials such as steel or aluminum, allowing them to withstand the high pressures and temperatures involved in the injection process.
- Steel Molds: These are the most durable and capable of producing a high number of parts over their lifetime, making them ideal for long-term projects.
- Aluminum Molds: These offer a lower initial cost and quicker turnaround time, making them suitable for prototypes and short production runs.
Why Should You Buy Injection Plastic Molds?
Investing in injection plastic molds can dramatically benefit manufacturers. Here are some of the reasons you should consider:
1. Cost Efficiency
One of the most significant advantages of buying injection plastic molds is cost efficiency. Although the initial cost of the molds can be high, the long-term savings are often worth it. Here’s how:
- Low Production Costs: Once the mold is created, the cost per part decreases significantly with mass production.
- Reduced Waste: Injection molding is highly efficient, producing less scrap plastic compared to other manufacturing methods.
2. High Precision and Quality
Injection molds provide exceptional precision, which is vital for industries requiring strict tolerances. Each mold is designed to produce identical parts that meet exact specifications:
- Complex Designs: Injection molding can handle intricate shapes and designs that may be impossible with other manufacturing techniques.
- Surface Finish: The process allows for a smooth surface finish, reducing the need for secondary operations like sanding or polishing.
3. Versatility
Another major benefit of buying injection plastic molds is their versatility. This manufacturing process can accommodate a wide range of materials, including:
- Thermoplastics: These can be melted and remolded multiple times, offering flexibility in design and production.
- Thermosetting Plastics: These become permanently hard after setting, providing durability for high-performance applications.
The Process of Acquiring Injection Plastic Molds
Choosing the right injection mold for your business comes with several steps:
1. Research and Development
Before making a purchase, conduct thorough research to understand your product requirements. Collaborate with your design and production teams to create a detailed product design that adheres to your specifications. This preliminary phase is critical for ensuring the success of the final product.
2. Selecting a Reputable Supplier
Once your design is complete, the next step is to select a supplier. At DeepMould.net, we excel in providing high-quality metal fabrication services. Factors to consider when choosing a supplier include:
- Experience: Look for suppliers with extensive experience in manufacturing injection molds.
- Customer Reviews: Check testimonials and reviews from previous customers to gauge reliability and quality.
- Technology Used: Ensure that the supplier utilizes state-of-the-art technology for mold production.
3. Pricing and Lead Times
After selecting a supplier, request a quote. Compare prices, keeping in mind that the cheapest option is not always the best. Consider factors such as quality, lead times, and delivery reliability. The lead time for mold production can vary significantly, often taking anywhere from a few weeks to several months, depending on the complexity of the design and the supplier's workload.
Quality Assurance in Injection Molding
Ensuring that your injection molds meet rigorous quality standards is vital. At DeepMould.net, we understand the importance of quality assurance in the injection molding process. Here’s what to look for:
1. Material Selection
The materials used to create molds can affect final product quality. Utilize high-quality, durable materials to ensure the longevity and effectiveness of your molds.
2. Precision Engineering
Each mold must be engineered for precision. Poorly designed molds can lead to defects in the finished product, leading to increased costs and time delays.
3. Regular Testing
Implement a routine testing schedule for molds to identify any issues early. This proactive approach can minimize downtime and reduce production costs over time.
Conclusion
In conclusion, buying injection plastic molds is a strategic investment that can greatly enhance manufacturing productivity and product quality. The ability to produce high volumes of precise parts efficiently not only streamlines operations but also helps businesses to stay competitive in an ever-evolving market.
At DeepMould.net, we specialize in providing superior metal fabrication services, ensuring that your injection molding needs are met with the highest standards of quality and efficiency. By choosing us, you are investing in a partnership that values excellence and innovation. Contact us today to learn more about how we can support your manufacturing goals and help you in your journey to acquire the right injection plastic molds for your business.