Unlocking the Potential of Seal Vacuum Press Technology
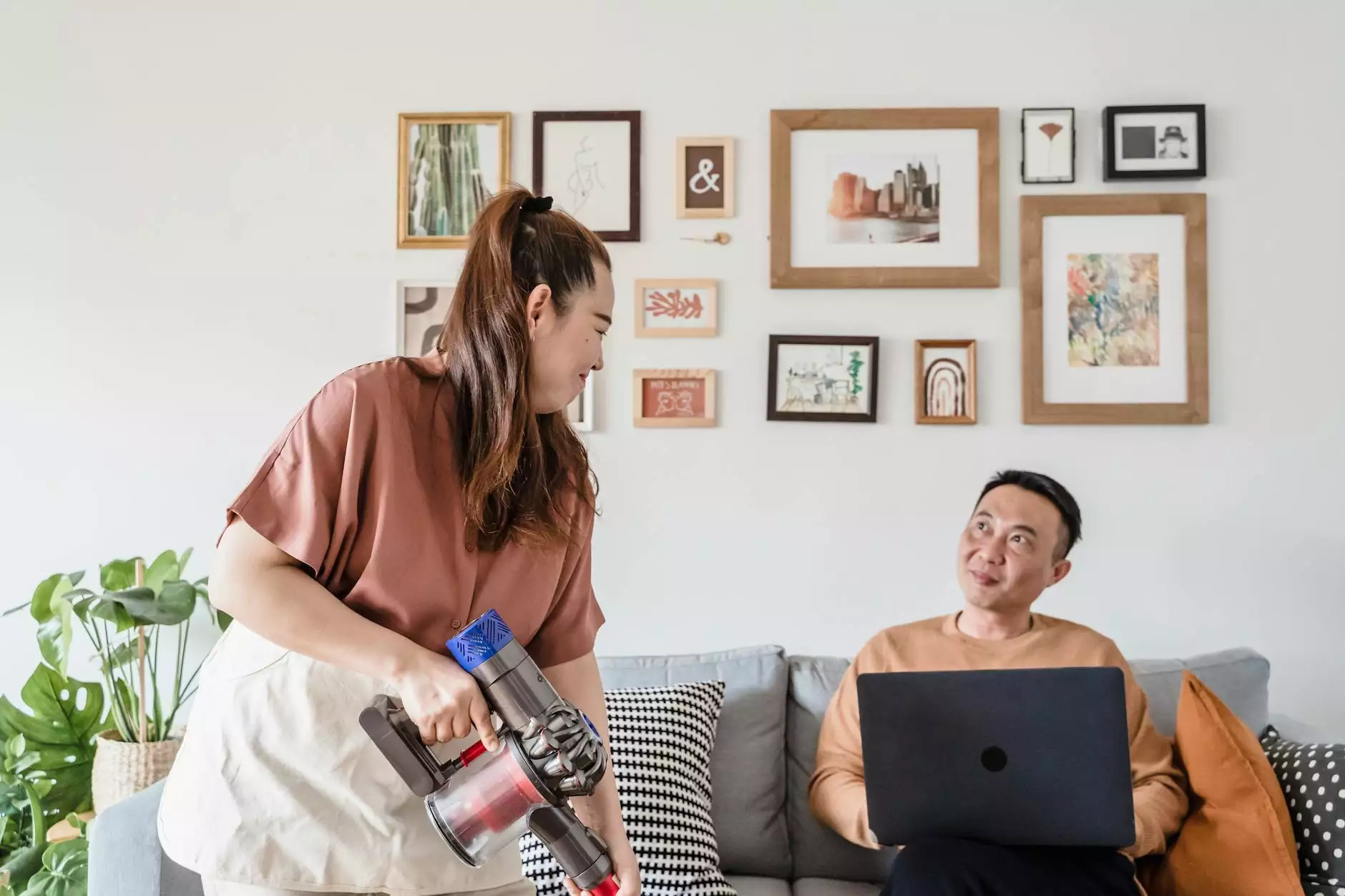
In the ever-evolving landscape of modern manufacturing and business, seal vacuum press technology has emerged as a crucial player. This advanced technology has revolutionized various industries by providing efficient solutions for encapsulation, lamination, and material handling. As we delve into the intricacies of this technology, we will explore different membrane types, essential components of a vacuum system, and how businesses can leverage these innovations for enhanced productivity and profitability.
Understanding Seal Vacuum Press Technology
The seal vacuum press is a powerful tool designed to create a vacuum environment that ensures optimal adhesion and bonding of materials. This technology is widely used in industries such as woodworking, composite manufacturing, and packaging. By removing air and moisture from the materials, the seal vacuum press creates a perfect environment for adhesives to cure and bond surfaces without imperfections.
The Core Benefits of Using Seal Vacuum Presses
- Enhanced Adhesion: The vacuum environment eliminates air pockets, resulting in stronger, more durable bonds.
- Improved Surface Quality: The application of pressure during sealing ensures a smooth and even finish.
- Time Efficiency: The curing time for adhesives is significantly reduced, leading to faster production cycles.
- Versatility: Seal vacuum presses can handle a wide range of materials, including wood, composites, and plastics.
Types of Membranes for Seal Vacuum Press
Choosing the right membrane is crucial for the effective operation of a seal vacuum press. Membranes determine the quality of the vacuum seal and can impact the overall performance of the system. Here, we’ll explore various types of membranes available in the market.
1. Silicone Membranes
Silicone membranes are known for their flexibility and resistance to high temperatures. They are commonly used in applications where heat is involved, making them ideal for bonding materials with thermal curing adhesives. The characteristics of silicone membranes include:
- High Temperature Resistance: Able to withstand temperatures up to 250°C.
- Durability: Resistant to wear and abrasion, leading to a longer lifespan.
- Excellent Elasticity: Provides a good seal and accommodates material expansion.
2. Natural Rubber Membranes
Natural rubber membranes are popular due to their excellent flexibility and sealing capabilities. These membranes are best suited for applications that require strong vacuum retention and are often used in woodworking and composite applications. Key features include:
- Good Adhesion Properties: Creates a tight seal, minimizing air leakage.
- Cost-Effectiveness: Generally more affordable option compared to synthetic alternatives.
- Resistance to Creeping: Maintains its shape and performance over time.
3. Rubber Membranes
Rubber membranes, commonly made from synthetic materials, provide excellent resistance to chemicals and moisture. They are widely used in industries that require a high level of precision and reliability. Benefits include:
- Chemical Resistance: Suitable for various industrial applications involving harsh chemicals.
- High Load-Bearing Capacity: Can withstand significant pressure without deforming.
- Long-Term Stability: Maintains performance over extended periods, ensuring consistent results.
Essential Components of a Seal Vacuum Press System
To achieve optimal performance from a seal vacuum press, understanding its components is vital. Here are the key parts that make up this sophisticated system:
1. Vacuum Pumps
The heart of any vacuum system, vacuum pumps create the necessary vacuum environment by removing air and moisture from the chamber. There are various types of pumps, including rotary vane pumps and membrane pumps, each serving different application needs.
2. Pressure Plates
Pressure plates are essential for ensuring even distribution of pressure across the materials being bonded. They help maintain a consistent vacuum seal and prevent material waste due to uneven pressure.
3. Control Systems
Modern seal vacuum presses are equipped with advanced control systems that allow users to monitor and adjust vacuum levels, temperature, and pressure settings. These systems increase operational efficiency and ensure quality results.
Business Opportunities with Seal Vacuum Press Technology
With the rising demand for efficient manufacturing processes, businesses that leverage seal vacuum press technology can stand out in competitive markets. Here’s how:
1. Customization and Scalability
Businesses can offer customized solutions based on client needs. By adapting vacuum press systems to specific applications, you can tap into niche markets and diversify your product offerings.
2. Expansion into New Markets
Industries like automotive, aerospace, and furniture manufacturing are increasingly adopting seal vacuum press technology. By investing in this technology, businesses can penetrate these lucrative markets and increase profitability.
3. Sustainability Initiatives
As companies strive for sustainability, using seal vacuum presses can lead to less material waste and energy consumption, aligning with eco-friendly practices. This can also enhance brand reputation and attract sustainability-conscious consumers.
How to Buy Membranes and Vacuum System Parts
To ensure the performance of your seal vacuum press, purchasing high-quality membranes and components is critical. Here are some tips on sourcing these essential parts:
1. Research Reputable Suppliers
Begin by searching for reputable suppliers who specialize in vacuum system parts. Look for companies that offer a range of products such as:
- Silicone membranes
- Natural rubber membranes
- Rubber membranes
2. Evaluate Product Quality
Before making a purchase, evaluate the quality of the membranes. Check for certifications and customer reviews to ensure reliability and durability.
3. Consider Pricing and Warranty
Price is an important factor, but it shouldn’t be the only consideration. Look for suppliers that offer competitive pricing and a good warranty, signaling confidence in their products.
The Future of Seal Vacuum Press Technology
As industries continue to evolve, the demand for efficient manufacturing processes will only grow. The future of seal vacuum press technology looks promising, with advancements in automation, smart technologies, and material science paving the way for new applications.
1. Automation and Smart Technologies
Integrating automation with vacuum press technology can streamline operations, reduce labor costs, and improve efficiency. Smart technologies will allow for better monitoring and control, ensuring optimal performance and quality.
2. Innovations in Membrane Materials
Research and development in new membrane materials can lead to improved performance and versatility. Innovations may yield membranes that are lighter, more durable, and resistant to a variety of substances.
Conclusion
Embracing seal vacuum press technology opens up vast opportunities for businesses willing to innovate and adapt. By understanding the importance of quality membranes, efficient vacuum systems, and leveraging the right components, companies can achieve remarkable productivity and profitability. As this technology continues to evolve, staying informed and agile will be key to maintaining a competitive edge in your industry.
For those looking to invest in this technology or enhance their existing processes, visiting vacuum-presses.com offers valuable insights and resources on purchasing high-quality membranes and vacuum system parts. Take the next step towards optimizing your business operations today!